Text Ulrich Kläsener ––– Fotografie
Wer das Drei-Mann-Start-up aus den 80ern mit dem heutigen mittelständischen Unternehmen von Weltruf vergleicht, merkt schnell, dass es nicht die Masse ist, die Teledoor Melle Isoliertechnik GmbH groß gemacht hat. Es war – und ist nach wie vor – der Anspruch des klassischen Variantenfertigers, für jeden Kunden die richtige Lösung in exzellenter Ausführung zu liefern und zu keinem Kunden „Nein“ zu sagen. Die Teledoor Melle Isoliertechnik GmbH fertigt seit über 30 Jahren vielfach erprobte und bewährte Kühl- und Tiefkühlzellen sowie Kühl- und Tiefkühlraumtüren. Wer aber, wie die Niedersachsen, bei der Kundenorientierung nicht den geringsten Abstrich macht, kann beim klassischen Engineering-to-Order Probleme bekommen: bei der Marge, in Sachen Wettbewerbsfähigkeit, auch teamintern, da komplexe Aufgaben eben auch Aufwand bedeuten. Der potenziert sich bei zunehmendem Auftragseingang, was Teledoor veranlasste, nach Effizienzpotenzialen zu suchen. Zumal man unternehmensintern feststellte, dass die Konstruktion mit ihren 27 CAD-Arbeitsplätzen zunehmend zum Flaschenhals wurde und es nicht mehr schaffte, die Produktion auszulasten.
PAIN POINTS IM FOKUS
Bei der Potenzialanalyse machte man drei Schwachstellen aus: den Bereich CAD, die Prozesse und die Strategie. Zunächst hinkte die Konstruktionsabteilung dem Auftragseingang hinterher, weil zu viel repetitive Arbeit sehr hohen und fehlerbehafteten Zeitaufwand bedeutete. Daniel Krämer, Leiter IT & Digitalisierung bei Teledoor: „Nur der geringste Teil der Arbeit bestand in ihrer eigentlichen Aufgabe: der Konstruktion.“ Ein Missverhältnis zwischen Aufwand und Ertrag bestand auch im Ersatzteilgeschäft, da es permanent über die Konstruktion freigegeben werden musste, damit die Standard-Schnittstellen zum ERP angesprochen werden konnten. „Außerdem mussten wir etwas unternehmen, weil wir uns unnötig den Datenbestand aufblähten“, führt Daniel Krämer aus. „Viele Bauteile waren identisch, hatten aber durch Kopieren im PDM-System mehrere Artikelnummern. Zuletzt fehlte es am Überblick und an einer klaren Linie, da bei einer Konstruktionsabteilung von über 20 Personen gewisse Standards verloren gehen.“ Der eigentliche „Elchtest“ war unterdessen die Kommunikation der Abteilungen untereinander, beispielsweise bei kurzfristigen Auftragsänderungen. Krämer ergänzt: „Die können im kompletten Chaos enden, wenn noch Datenredundanzen auftreten, beispielsweise vom Anlegen des Auftrags in Textform über die Umsetzung in eine CAD-Konstruktion bis hin zu den Infos für die Produktion.“
ZEITENWENDE IM ENGINEERING
Was tun? Krämer erinnert sich: „Schnell wurde klar, dass wir einen disruptiven Ansatz wählen mussten, um wirklich voranzukommen.“ Das bedeutete, dass Teledoor ganze Prozessketten auf den Prüfstand stellte, weniger einzelne Arbeitsschritte. Über das Thema Variantenkonstruktion im PDM/ERP-Segment stieß Daniel Krämer auf das Unternehmen Cideon, das als eines der wenigen Systemhäuser integrierte CAD-, PDM- und ERP-Expertise vorhält. „Uns reizte vor allem die Cideon These, dass das Engineering-to-Order-Prinzip keinen Widerspruch zur Automatisierung darstellen muss“, erläutert Krämer. Tatsächlich legten Cideon und Teledoor nach Erstgesprächen sofort los und waren keine acht Monate später dort angelangt, wo sie hinwollten: bei einem No-Touch-Prozess von Kundenanfrage bis Produktion, in dem die vollautomatisierte Konstruktion zumindest bei konfigurierbaren Standardprodukten keinen einzigen Handschlag mehr macht. Die in Rekordzeit ins Laufen gebrachte Configure-to-Order-Lösung basiert auf Cideon Conify. Das ist eine individuell konfigurierbare Softwarelösung, die die Vertriebs- und Engineeringdaten bei Teledoor verbindet und die beteiligten Systeme wie ERP, CAD und PDM integriert. Aus Prozesssicht wird das vom Vertrieb über die eingerichtete Benutzeroberfläche konfigurierte Produkt automatisiert als CAD-Datensatz ausgeprägt und anschließend PDM-konform gespeichert. Das Ganze im No-Touch-Modus, weil Dokumentationen, Stücklisten und Arbeitspläne automatisiert erzeugt werden und bis in die Auftragsabwicklung und Fertigung durchlaufen.
Daten & Fakten
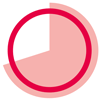
70 %
beträgt der Anteil der Aufträge, die Teledoor im Endausbau über den „No-Touch-Prozess“ abdecken will; die übrigen 30 Prozent gehen in die Konstruktion.
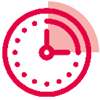
15 min
beträgt die Zeit von der Erfassung der Produkt-Parameter durch den Vertrieb bis zum Start der Fertigung.
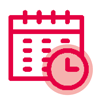
8 Monate
dauerte die Einführung des Configure-to-Order-Prozesses, über drei Monate schneller als von Teledoor erwartet.
ANDERS UND DEUTLICH BESSER
Der Weg zum Configure-to-Order war kein leichter, aber ein schlüssiger. Teledoor unterteilte das Projekt in drei Arbeitsschritte: Eingabe der Mutterelemente ins CAD, dann die eigentliche CAD-Automatisierung über iLogic, schließlich die Übergabe der Fertigungsunterlagen. Mit Cideon gestaltete Teledoor das intuitiv bedienbare Konfigurator-Cockpit für die Vertriebler im Hause. Schon nach acht Monaten „spuckte“ der neue Prozess das erste greifbare Produkt aus. Daniel Krämer war positiv überrascht: „Wir hatten anfänglich mit grob einem Jahr bis zum Erreichen einer produktiven Arbeitsumgebung mit Vollautomatisierung geplant.“ Daniel Krämer erläutert: „In der Praxis geht der Vertrieb auf ein Frontend im ERP, gibt in der Benutzeroberfläche die relevanten Produkt-Parameter ein und drückt aufs Knöpfchen. 15 Minuten später kann der Auftrag theoretisch unten auf der Maschine starten, ohne dass irgendjemand eingreift. Dafür haben wir früher, auch durch Verzögerungen im Prozess, teils bis zu 2 Wochen gebraucht.“ Mehraufwand durch Auftragsänderungen gebe es auch nicht mehr. „Und natürlich: Der Konstruktionsaufwand für, Stand heute, 50 Prozent unserer Standardprodukte reduzierte sich von 100 auf null Prozent. Eine direkte Auswirkung ist, dass wir durch das Eliminieren der Konstruktionszeit jetzt im Segment Tiefkühlzellen wieder wettbewerbsfähig sind. Wir bieten zu Top-Preisen maßgenaue Zellen von höchster Qualität an – manch anderer Anbieter nur Katalogzellen von der Stange.“ Im Endausbau wolle man 60 bis 70 Prozent aller Aufträge über den No-Touch-Prozess abdecken, 30 bis 40 Prozent gingen in die Konstruktion. Der händische Konstruktionsaufwand bleibe definitiv, auch wenn dieser über eine hybride Konstruktionsmethodik mit Namen „No Touch plus“ minimiert werden soll. Die Konstrukteure bei Teledoor sollen über den Konfigurator eine 70-prozentige Annäherung erreichen, um die restlichen 30 Prozent – meist deutlich komplizierter in der Realisierung – selbst zu konstruieren. Auffallen wird die neue Konstruktionsmethodik bei Teledoor so oder so weiterhin niemandem. Krämer: „Der Prozess ist so bündig integriert, dass nirgendwo Fragezeichen auftauchen.“ Die betriebswirtschaftliche Seite des Cideon Conify-Einsatzes bei Teledoor zeigt schon jetzt überragende Ergebnisse: „Das Projekt wurde definitiv so umgesetzt, wie wir uns das vorgestellt haben. Der ROI ist in einem Jahr erreichbar, das kann ich gut am Live-Dashboard nachvollziehen“, sagt Daniel Krämer und ergänzt: „Sogar das Budget wurde nicht ausgeschöpft, was bei solchen Projekten wirklich ungewöhnlich ist.“